Maintenance
(C) 2017 MAINELOGHOMEIPROFESSIONALSASSOCIATION.COM
Please note: We suggest that you review the license and insurance of any professional you use and we further suggest that you call references or review the ratings and reviews from their previous customers. When using our site, understand that it is your responsibility to select the professional you are interested in working with. Any contract or agreement you have with a contractor is between you and the company you select and does not involved our association. By using our website, you agree that should you have a dispute with any company, you must address such dispute directly with the business that performed the work. You also agree to release Maine Log Home Professionals Association (and our officers, directors, affiliates, employees, and agents) from any damages or claims that may arising out of or in any way connected with such disputes.
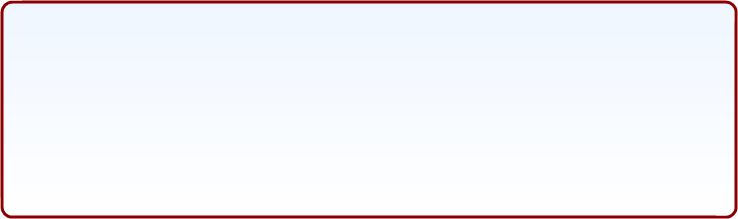
Log home maintenance is much more demanding than maintaining a conventional home and log homes have issues which need to be addressed differently than a stick-framed home. It is best to take a slow walk around the exterior of your home twice a year to assess the condition of your dwelling. Look carefully and critically at areas where water may be an issue, such as around doors and windows, dormer connections, roof junctions, chimney flashing and the end logs on your log home. Check the grounds closely.
The Maine Log Home Professional Association recommends log homes be professionally inspected every year or at least every 2 years.Some warranties for log homes require annual professional inspections to maintain the warranty. MLHPA recommend you read your warratny to determine what is required for regular inspections.
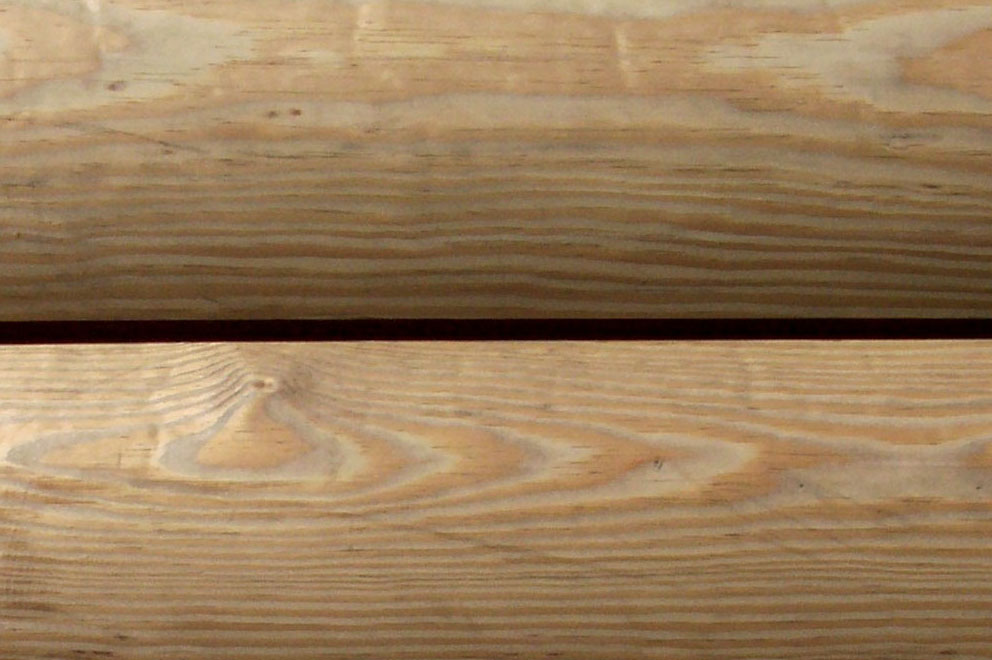
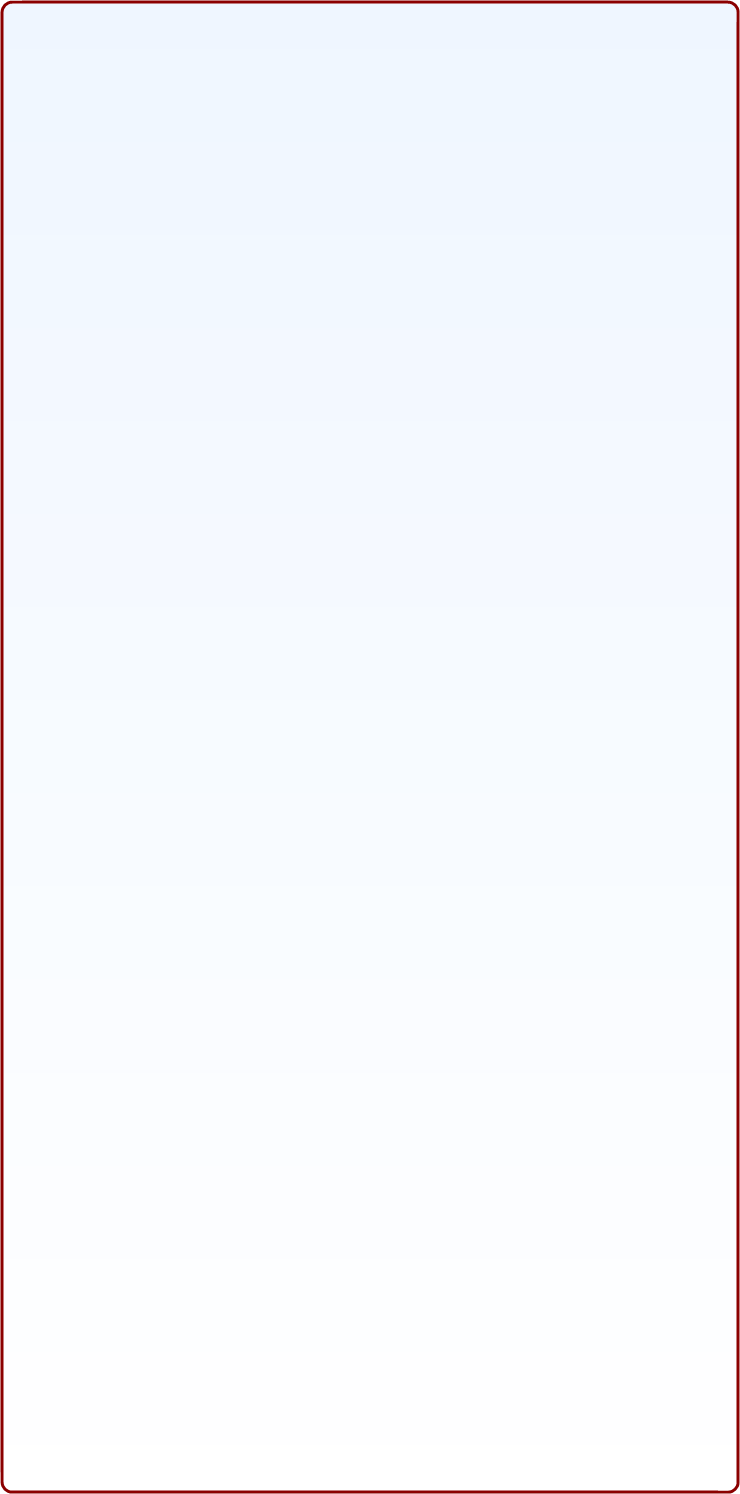
Cleaning
Look for dark patches where rain has splattered back on the logs and allowed mold or mildew to grow. This is best handled with a simple bleach/water solution mixed in a 50/50 ratio. Scrub the area gently with a soft brush wetted with the solution then hose it off and let dry for a couple of days before re-staining.
Iron Tannate Stains
If you have black stains on your wood that no amount of cleaning by your previous applicators can remove, it is possible that you have iron tannate stains.
Iron tannate stains are the result of a chemical reaction between naturally occurring wood tannates, water, and iron particles. These iron particles most often are introduced to the wood by roof water runoff, incorrect preparation of the wood using steel wool, or simply through the milling process.
This chemical process of iron tannate staining is not only multiplied by chlorine bleach but sometimes initiated by it.
Even more disturbing is that this form of staining is not visible until days or even months after stain is applied, and the appearance of these stains can only be removed or minimized after removal of any finishes, as the problem is on the wood itself. It is recommended that the sealer (lacquer, varnish, polyurethane) be removed prior to using oxalic acid to remove the iron tannate stains.
Caulking
Logs will tend to crack and check over time. Over the first year or two as they come into equilibrium with the local humidity and variation over the seasons the logs will swell, contract and check.
This is normal and will not affect the strength or integrity of your logs. For the first several years caulking may be a regular part of your log cabin maintenance routine as the logs settle down to moisture equilibrium.
It is a good idea to seal up the larger of these checks, anything over about a quarter of an inch to seal out water and bugs. Caulk these with caulk formulated for logs with good stretch and sealant capabilities.
For large checks you should first fill the cavity with backer rod (round foam strips) and then apply the caulk over this. This provides good adhesion for the caulk and the foam allows the normal expansion and contraction of the wood without affecting the caulks bond. Over time this area of log cabin maintenance becomes easier and easier.
Sealing
For large gaps such as around your window and door bucks we have found it best to use expanding foam. If you can feel the cold air coming in around your doors and windows you need to remove the trim boards and check that the bucks have been sealed. Log homes need to be re-sealed on a regular basis (on average every 3 to 5 years depending on product used and other factors)
If the existing finish has been properly maintained, it should never require stripping however if the existing surface has suffered damage (UV degradation, sealant failure, water absorption) applying the most expensive sealant will be a waste of time and money without repairing the damage to the logs.
The Sweep
When we refer to the Sweep of a log we are talking about the bowing.Bowing is NOT always a hazard and can be fine if the moisture levels are low that the shrinkage has stopped without harming the home
The Taper
The taper is the difference in diameter between the logs tip and the butt. Again this is not a hazard in the construction stability as long as the logs are alternating properly with the butt on one end and a tip on the other.
Stains/ Sealants
What are the "black specks" appearing on log walls, decks, and asphalt roof shingles? These are actually mature spore masses expelled from fruiting bodies of a fungus known as "shot gun" or "artillery" fungus. Some log homeowners choose to apply a clear sealer with no stain (pigment). If you do this, your logs are guaranteed to darken much quicker As a general rule, , clear sealers do not offer UV protection. Pigment is what offers UV protection., UV-Boost is an example of an additive which can be added to clear sealants to provide necessary UV protection. Interior sealing products are different than the exterior clear coat which is applied over the stain. Applying an interior grade acrylic gloss or satin will allow for light reflection and keep the logs much cleaner. When they do get dusty, they can be wiped clean with a damp towel or sponge much easier than with no clear coat. This application will also do a good job at preventing odors (pet, smoke, cooking) from absorbing into the logs. You can apply this product on bare wood or over a stain.
No stain or sealant can guarantee that mold or mildew will not grow on the exterior of your log home to man will prevent mildew or mold growth, regardless of whether they have a mildewcide mixed in or not. Dry wood is what prevents mold or mildew. Certainly, an additional dose of mildewcide which can be added to the stain will make it that much more difficult for mold/mildew to thrive. But it is no guarantee it won’t ever appear. There are 4 conditions necessary for the growth of mold/mildew. These are: the presence of food, moisture, oxygen and temperature. If any of these 4 conditions are eliminated, so will the conditions needed for mold/mildew to grow. The wood is the food source. We have no control over the temperature and we need oxygen. A quality stain and a clear coat finish will help prevent your logs from absorbing moisture. The magic number for moisture content in your logs is 19%. At 20% or higher, mold/mildew can accumulate. Mold/mildew is not generally damaging to wood, it is only unsightly and in most cases, can be cleaned off with relative ease.
Log end Seal
This is a product specifically designed to seal the porous ends of logs and should be applied. some old school contractors will tell you the opposite and they will say this is a good place for the moisture to exit the wood. The MLHPA recommends you ignore such advice and seal the ends of all logs
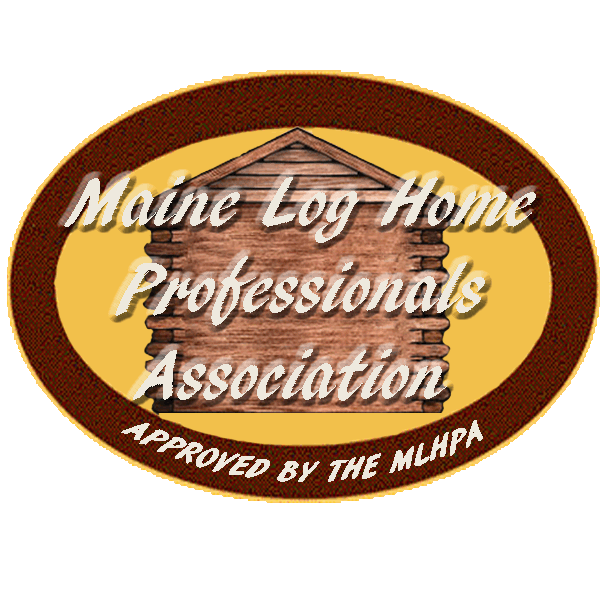